Wind Season: Maximizing Efficiency During High Production and Preventing Failures in Critical Components
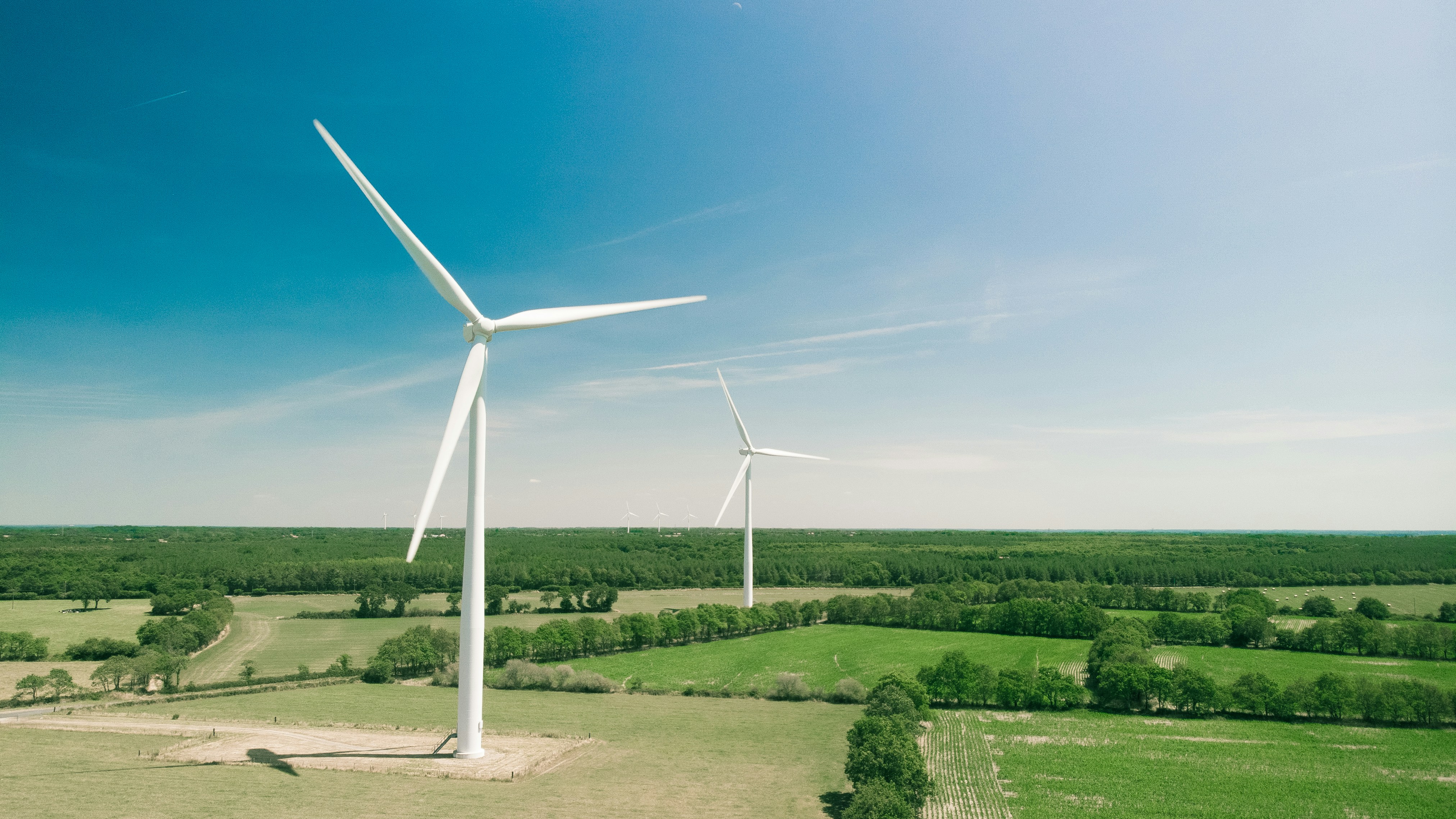
Wind energy is a rapidly growing sector, largely due to favorable geographic and climatic conditions. The wind season is characterized by stronger and more consistent winds, making it a crucial period for maximizing energy production. However, alongside increased production come challenges that require effective management and advanced technologies to ensure wind turbines operate at their peak without experiencing damage or failures.
Efficiency during the wind season depends not only on the natural potential available but also on the operators' ability to implement strategies that optimize turbine performance while avoiding operational issues.
The impact of wind season on energy production is significant. During this period, a substantial increase in energy generation can often be observed, surpassing the output of off-season months. However, to fully capitalize on this potential, efficient management involving constant asset monitoring and the application of preventive maintenance is essential.
Failures in critical components, such as blades and turbine transmission systems, represent one of the biggest risks during the wind season. These failures can result in unexpected shutdowns, which not only interrupt energy production but also lead to high repair costs and revenue loss. Therefore, preventing these failures is a fundamental aspect of wind farm operations during the wind season.
Challenges During the Wind Season
Despite the exceptional opportunities for energy generation during the wind season, it presents several challenges for wind farm operators. One of the primary challenges is the increased wear on turbine components due to constant exposure to high-intensity winds. While these winds are crucial for energy production, they place greater demands on blades, bearings, and transmission systems, accelerating wear and increasing the likelihood of failures.
Another significant challenge is the need for constant and precise monitoring. During the wind season, turbine operating conditions change rapidly, and operators must have real-time access to data to make informed decisions. Without a robust monitoring system, failures may go unnoticed until they escalate into major problems, resulting in production interruptions and increased operational costs.
Moreover, mechanical stress on turbine components during the wind season can lead to a variety of mechanical failures. For example, turbine blades, which are constantly subjected to variable aerodynamic forces, can develop micro-cracks that, if not detected in time, may result in catastrophic failures. Likewise, bearings and gears in transmission systems can suffer from fatigue due to continuous stress, causing unplanned downtime.
Preventive maintenance should occur before the high wind season to minimize issues during this critical time. By conducting regular inspections and utilizing advanced monitoring tools, operators can identify signs of wear or damage before they become severe problems. This not only helps prevent unexpected failures but also extends the life of components, ensuring turbines can operate efficiently throughout the season.
Strategies to Maximize Production Efficiency
Maximizing the efficiency of wind energy production during the wind season involves implementing strategies that leverage favorable conditions while mitigating the risks associated with increased production. One such strategy is the use of real-time monitoring tools. These tools allow operators to closely monitor turbine performance, identifying any anomalies or drops in efficiency as they occur.
Real-time monitoring is especially important during the wind season because turbine operating conditions can change quickly. With the ability to visualize real-time data, operators can adjust operations as needed to ensure turbines are always operating at optimal levels. For example, if a turbine is operating outside normal parameters, operators can schedule an intervention during a low-wind window, adjusting settings to optimize performance and prevent damage.
Additionally, data analysis plays a crucial role in optimizing production during the wind season. By analyzing historical and real-time data, operators can identify behavior patterns that indicate potential problems. For example, a gradual drop in turbine efficiency may signal the onset of wear in bearings or blades. By identifying these patterns early, operators can schedule preventive maintenance before the issue worsens, thereby avoiding unplanned downtime.
Another effective strategy is using performance forecasts based on meteorological and operational data. These forecasts allow operators to anticipate changes in wind conditions and adjust turbine maintenance schedules accordingly.
Integrating these strategies into a holistic management approach is essential to maximize efficiency during the wind season. Platforms like Delfos offer a comprehensive solution, combining real-time monitoring, data analysis, and forecasting to provide operators with all the tools needed to optimize wind energy production.
Preventing Failures in Critical Components
Preventing failures in critical components is a major concern during the wind season, especially as extreme operating conditions can accelerate wear and increase the probability of failures. To address this challenge, wind farm operators should adopt a proactive approach that combines preventive maintenance with predictive technologies.
Preventive maintenance involves conducting regular inspections and replacing components before they fail. This approach is essential before the wind season, as constant stress on components can lead to sudden failures, which, if not prevented, can result in extended downtimes and high repair costs.
In addition, the use of predictive models to monitor the condition of critical components allows operators to identify potential problems before they escalate into serious failures. These models use historical and real-time data to predict when a component is likely to fail, enabling operators to schedule preventive maintenance more efficiently.
The application of advanced monitoring technologies, such as vibration sensors and oil analysis, can provide valuable insights into the condition of critical components. Vibration sensors, for instance, can detect anomalies in bearing operation, indicating the need for maintenance before a failure occurs. Similarly, oil analysis can reveal contamination or lubricant degradation, which are signs of internal wear in transmission systems.
Therefore, combining preventive maintenance and predictive monitoring is the best strategy to avoid failures in critical components during the wind season. By adopting these practices, operators can ensure their turbines operate efficiently and reliably, maximizing energy production and minimizing maintenance costs.
Using Advanced Analytics for Monitoring and Decision-Making
The use of advanced analytics for monitoring and decision-making is one of the most effective approaches to ensure operational efficiency during the wind season. Advanced analytics enable wind farm operators not only to monitor turbine performance in real time but also to gain deep insights that can be used to improve operations and prevent failures.
Platforms like Delfos offer a comprehensive solution for data monitoring and analysis. These platforms collect and analyze data from various sources, including sensors installed on turbines, SCADA systems, and meteorological data. By integrating this information, the platform provides a holistic view of turbine performance, allowing operators to quickly identify any issues and take corrective actions.
Additionally, advanced analytics can be used to develop predictive models that help anticipate failures before they occur. These models use machine learning techniques to analyze patterns in historical and real-time data, identifying signs that a component is about to fail. By predicting these failures in advance, operators can schedule preventive maintenance more efficiently, avoiding unplanned downtime.
Another benefit of advanced analytics is the ability to optimize turbine operations in real time. For example, the platform can analyze meteorological data to predict changes in wind conditions and automatically adjust turbine settings to maximize energy production. This ensures that turbines are always operating at optimal levels, regardless of external conditions.
Recommendations
The wind season offers a unique opportunity to maximize wind energy production, but it also presents challenges that require efficient management and the use of advanced technologies. Implementing an integrated approach that combines real-time monitoring, preventive maintenance, and advanced analytics is essential to ensure operational efficiency and asset safety during this critical period.
Wind farm operators are strongly encouraged to adopt solutions like those offered by Delfos, which provide all the necessary tools to monitor and optimize turbine performance in real time. By investing in cutting-edge technologies and a proactive management approach, companies can ensure they are fully capitalizing on the wind season's potential while protecting their assets from failures and maximizing the profitability of their operations.
Book a meeting
Let's connect and forge new partnerships
Custom Renewable Energy Solutions
Contact us today to discuss your renewable energy needs and find the perfect solution for your business.